티스토리 뷰
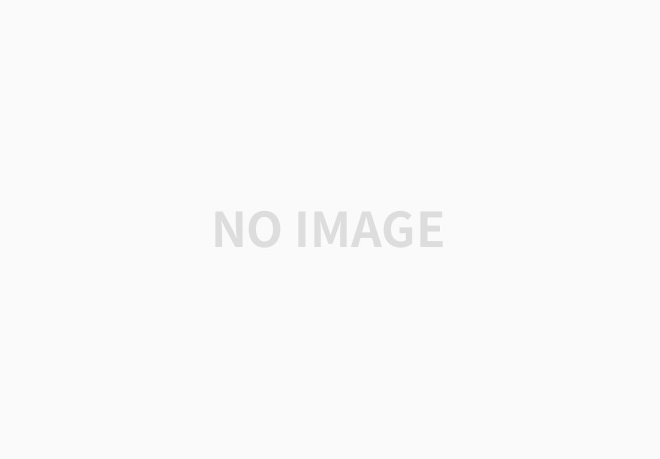
전자빔 용접 개념
전자빔 용접은 용접봉이없고 산화가 쉽지 않으며 공정 반복성이 좋고 열 변형이 적다는 장점 때문에 항공 우주,원자력, 국방 및 군사 산업, 자동차, 전기 및 전기 기기와 같은 많은 산업에서 널리 사용됩니다. 전자빔 용접의 기본 원리는 전자총의 음극이 직접 또는 간접 가열에 의해 전자를 방출한다는 것입니다. 전자는 고전압 정전기 장에 의해 가속 된 다음 전자기장에 의해 집중되어 매우 높은 에너지 밀도의 전자빔을 형성합니다. 공작물에 충격이 가해지면 거대한 운동 에너지가 열 에너지로 변환되어 용접 장소에서 공작물을 녹여 용융 풀을 형성하여 공작물의 용접을 실현합니다.전자빔 용접의 기본 원리에 따라 서방 국가들은 1970 년대 후반 바이메탈 톱 밴드 전자빔 용접을 위한 새로운 공정 생산 라인을 연구 개발하여 전통적인 일반 고속 쇠톱 밴드 생산 공정을 대체하여 많은 고속 강철을 절약하고 톱을 개선했습니다. 벨트의 수명.바이메탈 쏘 밴드는 탄성이 좋은 스프링 강과 절삭력이 강한 고속 강을 전자빔 용접하여 얻은 새로운 형태의 쏘 밴드입니다.1980 년대 후반, 중국은 국내 시장의 급속한 발전에 대한 요구를 충족시키기 위해 독일에서 여러 생산 라인을 연속적으로 도입했지만 시장 요구 사항을 완전히 충족하지 못했습니다.전자빔 용접에는 기계,진공,고전압 및 전자기장 이론,전자 광학,자동 제어 및 컴퓨터 및 기타 다 분야 기술이 포함되어있어 일반 국내 제조업체가 어렵고 도입 비용이 비쌉니다.고전압 전원 공급 장치는 바이메탈 톱 밴드 용접 장비의 핵심 기술 중 하나이며 주로 전자총에 가속 전압을 제공하며 그 성능은 전자빔 용접 공정과 용접 품질을 직접 결정합니다.이러한 이유로 많은 전자빔 용접기 제조업체 및 연구 기관은 고전압 전원 공급 장치의 신뢰성, 고전압 보호 및 고전압 점화가 용접물에 미치는 영향에 대한 연구를 수행했으며 이에 따라 다양한 요구 사항을 충족하는 더 높은 성능의 고전압 전원 공급 장치를 제조했습니다. 전자빔 용접기의 필요성. 바이메탈 용접에는 평행 이음새가 필요하기 때문에 바이메탈 톱 밴드 용접에는 고전압 전자빔 용접기 (100kV 이상)를 사용해야하므로 고전압 전원의 개발 및 연구가 필요합니다.전자는 일종의 물질의 기본 입자이며 일반적으로 핵 주위를 고속으로 회전합니다.전자에 일정량의 에너지가 주어지면 전자는 궤도에서 튀어 나올 수 있습니다.음극을 가열하면 자유 전자가 방출되어 구름이 형성되고 전압이 30 ~ 200kv로 증가하면 전자가 가속되어 양극쪽으로 이동합니다.
기술 요구 사항
다른 유형의 고전압 전원 공급 장치와 비교할 때 전자 빔 용접기 용 고전압 전원 공급 장치는 기술적 특성이 다릅니다.외국 전자빔 용접기 제조업체의 공장 출하 표준, 독일 DIN 표준 및 중국 전자빔 용접기의 기술 요구 사항에 따라 전자빔 용접기의 고전압 전원 공급 장치 요구 사항은 다음과 같습니다.전자빔 용접기 용 고전압 전원 장치의 기술적 요구 사항은 국내외에서 통일되지 않았습니다. 일부 제조업체의 기술 요구 사항에 따라 주요 기술 요구 사항은 리플 계수와 안정성입니다. 리플 계수는 1 % 미만이어야하며 안정성은 1입니다. 거의 모든 전자빔 용접기 제조업체가 이러한 요구 사항을 제시했습니다. 그중 독일 PTR 회사는 상대 리플 계수가 0.5 % 미만, 안정성이 0.5 %, 반복성 요구 사항이 0.5 % 미만인 고압 유형에 대한 기술 요구 사항도 제안했습니다.위의 요구 사항은 전자 빔 스폿 및 용접 프로세스에 의해 결정됩니다. 또한 독일 Pro-beam Group은 전자빔 경화로 만든 강철의 탄소 함량이 0.18 % 이상이어야한다고 제안했으며 진공의 장점은 어닐링 후 변색이없고 수소 취성이 없으며 깊이가 0.1-1.7mm이고 표면 용해가 없다는 것입니다.
작동 원리
- 고전압 전원 공급 시스템: 계통 전압은 흐름 억제 회로를 통해 한 번 고전압 승압 정류기 변압기로 들어가고 두 번째 단계는 약 100kV로 부스트됩니다. 이 AC 고전압은 12 상 정류 및 필터링을 거쳐 약 160kV의 DC 고전압을 얻어 고전압 진공관과 전자총에 인가합니다. 고전압 전자관은 작동 중 40kV의 전압을 견디므로 전자총에 인가되는 고전압은 120kV입니다.고압 진공관은 고압 출력을 조절하고 안정화하는 데 사용됩니다.
고전압 전원 공급 장치의 주회로 원리에 따르면 전원 공급 장치는 고전압 측에서 직접 조정되는 전형적인 직렬 형 고전압 DC 조정 전원 공급 장치라고 알려져 있습니다. 주 회로는 주로 과전류 억제 회로, 고전압 부스트로 구성됩니다. 필터링, 저항 용량, 과전압, 과전류 보호 회로, 고전압 진공관 조정 회로 등 고전압 승압 정류기 변압기, 고전압 정류기 회로, 고전압 필터 및 저항 커패시턴스 및 과전압, 과전류 보호 회로는 모두 오일 탱크에 배치되며, 작동 중 전원 공급 장치 본체의 절연 및 방열 요구 사항을 보장하기 위해 변압기 오일로 채워집니다. 고전압 전원 공급 장치는 지속적으로 작동해야하므로 작업 중 열을 적시에 방출 할 수 있도록 수냉 시스템도 연료 탱크 내부에 설계되었습니다.전원 공급 장치의 다양한 회로의 구성과 기능은 다음과 같습니다. 과전류 억제 회로는 3 상 브리지 정류기 회로와 초크 인덕터로 구성됩니다. 부하에 과전류가 있거나 전원 공급 장치가 갑자기 켜지고 변압기의 전자기 과도 과정에 의해 발생하면 큰 전류가 나타납니다. 다른 현상이 발생할 경우 과전류 억제 회로는 전원 공급 장치 내부의 과전류를 효과적으로 제한하여 전원 공급 장치를 손상으로부터 보호 할 수 있습니다.원칙은 인덕터 전류가 갑자기 변할 수없는 특성을 사용하여 과전류를 제한하고 고전압 변압기가 손상되지 않도록하는 것입니다.일반적으로 3 상 전류는 균형을 이루며 과전류 억제 회로로 흐르는 전류는 매우 작습니다.정류기 변압기의 2 차측은 4 개의 코일이 스타 형과 삼각형의 두 그룹으로 연결되어 있습니다.각 그룹이 정류 된 후 12 상 DC 맥동 전압이 직렬로 얻어 져 그리드로의 고조파 전류 오염을 줄이고 필터링 커패시턴스를 줄이고 전력 공급을 줄이는 데 도움이됩니다. 리플 팩터는 전원 공급 장치 자체의 성능을 향상시킵니다.정류기 회로는 고전압 실리콘 스택과 저항-커패시턴스 소자로 구성되어 있으며, 저항-커패시턴스 회로는 주로 고전압 실리콘 스택에서 발생하는 과전압을 방지하고 고전압 실리콘 스택이 손상되지 않도록합니다.전류 제한 저항과 보호 저항은 전원 공급 장치의 정상 작동을 보장하기 위해 전원 공급 장치 내부의 과전류 및 과전압을 제한하는 데 사용되며 저항은 더 높은 내전압 수준과 더 큰 가열 전력을 가져야합니다.전원 공급 장치가 외부에서 단락되면 보호 회로가 가능한 한 짧은 시간에 작동하여 관련 부품이 손상되지 않습니다.고전압 필터 커패시터는 DC 출력에서 AC 맥동 구성 요소를 필터링하여 전자총과 조정 튜브에 적용되는 전압이 평탄한 지 확인합니다.커패시터 코어는 고전압 연료 탱크에 직접 배치되어 전원 공급 장치 본체의 볼륨을 줄일 수 있습니다.조정 튜브는 160kV의 작동 전압을 가진 다극 고전압 진공관으로 주로 양극, 제어 전극, 1, 2, 3 양극으로 구성됩니다. 조정 튜브의 양극은 고전압 정류기의 양극에 연결되고 조정 튜브의 음극은 통과합니다. 빔 전류 샘플링 저항은 접지에 연결됩니다.조정 튜브는 제어 회로의 작용에 따라 고전압 출력을 자동으로 조정하고 안정화 할 수 있습니다.고전압 조절 관의 작동 전압이 높기 때문에 작동 중에 많은 열이 발생하기 때문에 특수 방열 장치가 설계되었습니다.
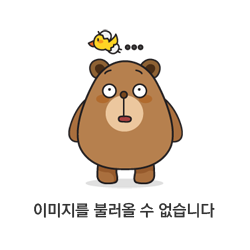
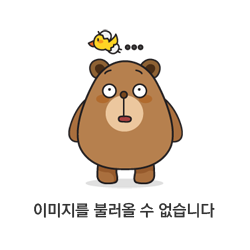
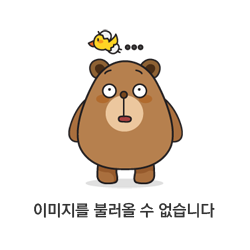
고전압 측에서는 고전압 DC 전원 공급 장치의 출력이 고전압 진공관에 의해 조절되어 출력 특성이 좋고 리플 계수가 작고 안정성이 높습니다.조정 튜브가 필터 커패시터를 분리하기 때문에 과전압 보호를 위해 전원 공급 장치가 차단되면 커패시터의 에너지가 공작물로 누출되지 않고 공작물이 손상되지 않습니다.바이메탈 톱 밴드 생산 라인에서 실제로 작동 한 후 전원 공급 장치의 기술 지표가 생산 라인의 프로세스 요구 사항을 충족합니다.
'정보' 카테고리의 다른 글
플라즈마 아크 용접 (0) | 2020.09.10 |
---|---|
오버 헤드 용접 (0) | 2020.09.08 |
일렉트로 슬래그 용접 (0) | 2020.09.02 |
플라스틱 레이저 용접 (0) | 2020.08.31 |
레이저 용접 (0) | 2020.08.26 |